Chemical Inhibitor Injection
Systems and processes can suffer from performance issues related to corrosion or scale buildup in components such as piping, heat exchangers, pumps, and valves.
Corrosive decay can affect the safety and integrity of a system by degrading materials and components. Scale buildup may affect the efficiency of a process by decreasing flow passages and potentially blocking all or part of a process stream. Heavy scale buildup can break off and clog or damage downstream equipment.
BETE spray nozzles coupled with injection lances maximize efficiency in inhibitor injection applications as they atomize and distribute the inhibitor liquid into the vessel or process stream to prevent corrosion or scale formation.
________________________________________________________________________________________________________________________
Scavenger Chemical Injection
Scavengers are liquid chemicals that neutralize and remove small amounts of hazardous or problematic compounds from bulk fluid streams, typically hydrogen sulfide (H2S). H2S removal is critical to prevent expensive infrastructure damage and ensure compliance with environmental and safety regulations.
BETE spray nozzles atomize and distribute the neutralizing liquid into the process stream, increasing the reaction surface area for H2S and other problematic compounds in the pipeline.
Common Uses And Industries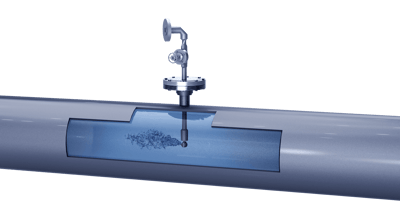
- Natural gas and oil pipelines
- Heat exchangers
- Injection of inhibitors such as MEG (mono ethylene glycol) and methanol
- H2S removal from gas streams
- Natural gas pipelines and processing plants
- Petrochemical Processing Industry
- Chemical Processing Industry
- Pollution Control Industry
________________________________________________________________________________________________________________________
Important Factors to Consider When Selecting a Chemical Spray Injection Nozzle:
Inhibitor density and viscosity
Process pipe/vessel size, velocity, pressure, temperature, and fluid composition
Available installation ports and required clearance diameters:
- In general process piping applications, a minimum of 3-5 pipe diameters of straight length upstream and 5-10 pipe diameters of straight length downstream are recommended to ensure spray dispersion
Required materials of construction for corrosive environments
Ease of maintenance/replacement:
- Retractable lances allow for quill/lance removal while leaving the process online
Required inhibitor flow rate
Available pressure drop (∆P) across the nozzle:
- ∆P = supply pressure at nozzle inlet – process pressure outside nozzle