Cool Your Cans
Enhance Your Aluminum Can Production with Efficient Coolant Filtration
Filtering Out Variability
Reduce aluminum loadings and tearoff.
Improve your production process.
With millions of identical parts being produced daily, even minor improvements can significantly impact overall process yield. 3M High Flow Filter System is designed for high performance and ease of operation, delivering a high flow filter within a compact housing design. This system is an essential component of the can manufacturing process, ensuring the reduction of aluminum loadings and tear-off, as well as minimizing defects, contaminant buildup, and dimensional variations.
The Can Manufacturing Process
- Uncoiler: This machine unwinds the aluminum coil into the lubricator.
- Lubrication: The lubrication step applies a thin film of lubricant to the aluminum sheet before feeding the metal into the stamper, which cuts out circular aluminum blanks.
- Cupper: Circular aluminum blanks are then fed to the cupper, responsible for forming the aluminum cups.
- Bodymakers: The bodymakers play a crucial role by deep-drawing the aluminum cups into aluminum cans at high speed and with very tight tolerances.
Reduce aluminum loadings
Maximize your operational efficiencies with 3M High Flow Filters:
![]()
|
Reduce defects Reduce contaminant buildup, streaking and dimensional variations.
|
|
Reduce production downtime Reduce tear off rate, extend tool life. |
![]()
|
Reduce labor Reduce number of filters and frequency of changeouts. |
![]()
|
Increase plant capacity Reduce tearoffs, increase production yield |
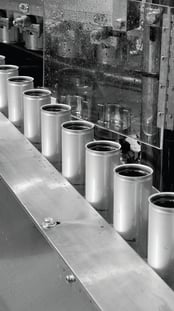
Minor variations.
Multiplied by millions.
Aluminum loadings, corrosion by-products and environmental contaminants are generated during the drawing process and carried away by the coolant. Without proper filtration, these particles can impact quality, increase tearoff , and limit production yield. To improve your manufacturing process and sustainability, 3M has an effective solution that results in cost reduction and labor savings.
Discover a cool way to improve efficiency.
3M High Flow Filter System
3M High Flow Filter System is the key to optimizing your can manufacturing process. It offers numerous advantages, including:
- Reduced footprint
A reduced footprint, taking up as little as one-half the size of competitive filter housings for a given flow rate. This results in lower capital investment costs and valuable plant space savings. - Ergonomic design
An ergonomic design, with a horizontal housing design and cartridge handle that enables quick and easy installation and removal while reducing changeout time and worker exposure. - Fewer filters required
Fewer filters required due to a highly efficient design, helping to reduce changeout times and disposal costs.
![]()
|
![]()
|
3M High Flow Filters
3M filters feature a "twist-to-lock" cartridge sealing mechanism, ensuring a positive seal and making cartridge installation and removal easier. These filters are constructed from polypropylene, compatible with canning industry coolants. The compound radial pleat design helps maximize the usable surface area of each filter while offering a high loading capacity.
![]() “Twist-to-lock” cartridge sealing mechanism |
![]() Ergonomic design |
Provides positive seal. | Handle makes cartridge installation and removal easier. |
Polypropylene construction: Compatible with canning industry coolants. Compound radial pleat design: Helps maximize the usable surface area of each filter while offering a high loading capacity. |
![]() |
3M High Flow Series Filter Systems
The 3M High Flow filter product family includes filter housings constructed of 316L stainless steel for the housing body and 316 stainless steel for the flanges and cartridge plug base. For can manufacturing, the 7-round variation of the 60" housing (7HF60) is best suited for meeting performance goals. |
![]()
|
Fewer cartridges. Smaller footprint. Faster change-outs.
Comparison of Required Filter Cartridges and their Housing Diameters
3M High Flow Filter System offers a clear comparative advantage, requiring fewer cartridges, occupying a smaller footprint, and allowing faster change-outs compared to conventional filter options. With 3M's system, you can achieve better results with just 7 cartridges in a 24" (610mm) diameter housing.
Conventional 2.5" (63.5mm) depth cartridges | Conventional 2.5" (63.5mm) pleated cartridges | 3M High Flow Filter System |
![]()
|
![]()
|
![]()
|
120 Cartridges in a 36" (914mm) diameter housing | 85 Cartridges in a 30" (762mm) diameter housing | 7 Cartridges in a 24" (610mm) diameter housing |
3M™ High Flow Filter Multi-Around Cartridge Housing, Model 7HF60
Housing Model |
Housing OD (in/mm) |
Inlet & Outlet Flange Size (in/DN) |
Vent & Drain NPT (in/mm) |
Empty Weight (lbs/kg) |
Housing Dimension, approximate length x width x height (in/mm) |
7HF60 (BHAACC) |
22/560 | 12/300 | 1/25.4 | 1084.7/492 | L – 100.2/2545 W – 22.1/560 H – 39.4/1000 |
3M High Flow Filter Specifications
For can manufacturing, 3M High Flow HFM Series 60" Filter Cartridges are the recommended solution to meet performance requirements.
- Filter media
3M High Flow filters are manufactured from melt blown polypropylene microfiber media, providing high particle
removal efficiency with broad chemical compatibility. - O-rings
For the 3M High Flow HFM Series Filters, O-rings are available in the standard nitrile.
3M High Flow Filter System Construction
In the can manufacturing industry, optimizing operational efficiency is critical. 3M High Flow Filter System, combined with expertly designed filter cartridges and filter housings, can make a substantial difference in your production process. With a maximum forward differential pressure of 50 psid and a recommended change-out differential pressure of 35 psid, 3M filter system ensures that your operations run smoothly and productively.
Filter micron rating (microns) | HFM 5μm Nominal |
Filter media, center core, end caps, outer sleeve | Polypropylene |
Sealing o-ring options | Nitrile |
Cartridge Dimensions
Inside diameter (nominal) | 3" (76.2mm) |
Outside diameter (nominal) | 6.5" (165mm) |
Cartridge length (nominal) | 60" (1524mm) |
Operating Conditions
Maximum forward differential pressure | 50 psid @ 68°F (3.4 bar @ 20°C) |
Recommended change-out differential pressure | 35 psid @ 68°F (2.4 bar @ 20°C) |
Enhance your can manufacturing process today with 3M's High Flow Filter System, featuring filter cartridges, and the latest in coolant filtration technology.
Contact us to explore the ideal solution for your unique needs and requirements.