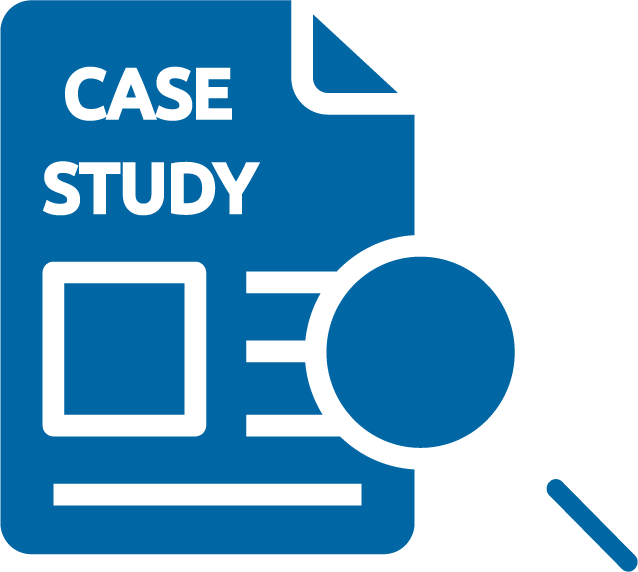
Price Pump Seal-less Mag Drive Pumps Eliminate Solvent Leakage for a Steel Coil Coater
The Challenge: Repeated Mechanical Seal Failures Caused Coating Solvent to Leak
The customer is Canada’s largest steel coil coater and operates two coating lines that can accommodate numerous paint systems and over 1,000 colours. These coating lines currently paint over 200,000 tonnes of steel annually, serving customers in various markets, including residential and commercial construction.
The customer’s pump system transfers a MEK (Methyl Ethyl Ketone) with some Xylene, Toluene and Benzene solvent from a charge tank into the plant as part of their painting and production process.
In this application, MEK is drawn from the charge tank into the plant as needed, which means the pumps involved in the process have to stop and start multiple times an hour to maintain the required pressure in the transfer tank (45 PSIG). This caused constant mechanical seal failures on these pumps, causing MEK to leak into the environment in an explosion-proof area.
This resulted in the following significant issues for the plant:
- Safety concerns for plant operators
- Ongoing containment requirements to prevent a negative environmental impact from the leaked chemical
- Loss of Production due to the downtime
- Increased Maintenance and Chemical costs
The Solution: A Seal-less Solution Using a Magnetic-Drive Centrifugal Pump
Our pump application expert worked with the customer and our engineering team to find a seal-less pump solution to prevent leakage altogether.
A Price Pump 2MS75MD Mag-Drive pump with a VFD and control panel was selected and installed to solve the customer’s problem.
The Result: Another Leaking Problem Solved
The results were a resounding success. With the new Pump and VFD and control panel installed, the pump is still in operation and working well over a year later with no leaks and minimal routine maintenance.
The benefits to the customer are:
- The seal-less design eliminated any leakage issues – saving the customer thousands of dollars/per year in lost chemical costs.
- The pump is designed to withstand caustic or corrosive substances which reduces maintenance requirements and helps save the customer with service and parts costs
- Reliable pump operation that reduces downtime and improves operational efficiency. Less downtime = more production.
- Improved safety for operators and plant personal
- Less negative impact on the environment due to no leaks
Pump Technology Used
We used a Price Pump Mag-Drive pump (Model 2MS75MD) with a VFD and control panel to solve the customer’s problem.
Pump specs
- Minimum Recommended Flow: 2 GPM (7.5 LPM)
- Max. Working Pressure: 300 PSIG (21 bar)
- Max. Solids Size: 0.03” (0.762 mm)
- Max. Temperature: 350 °F (177°C)
- 3/4” x 1” FNPT Suction / Discharge Ports
- 316 SS Construction
- PTFE O-rings
- Carbon Bushings
- 5” Impeller Diameter
- 5 HP, 3600 RPM Explosion-Proof Motor
How a Magnetic Drive (Mag-Drive) Pump Works
- Unlike a traditional centrifugal pump, a magnetic drive pump uses a magnetic field to rotate the pump impeller instead of a direct drive connection between the impeller and the motor.
- There’s an outer magnetic bell housing mounted on the end of the pump shaft and aligned on the outside of the rear casing. Inside the pump, a smaller magnet rides on an internal shaft and bushing assembly that’s connected to the pump’s impeller.
- When the pump motor starts, the outer bell housing rotates while affecting the inner impeller magnet. As both magnets turn together, their magnetic field rotates the impeller, which displaces the fluid.
Related Products
Talk to one of our Experts
Reach out to our team of Spraying, Pumping, Filtering, Valve, and Systems Specialists today. We know we can help you with any municipal or industrial application challenges.