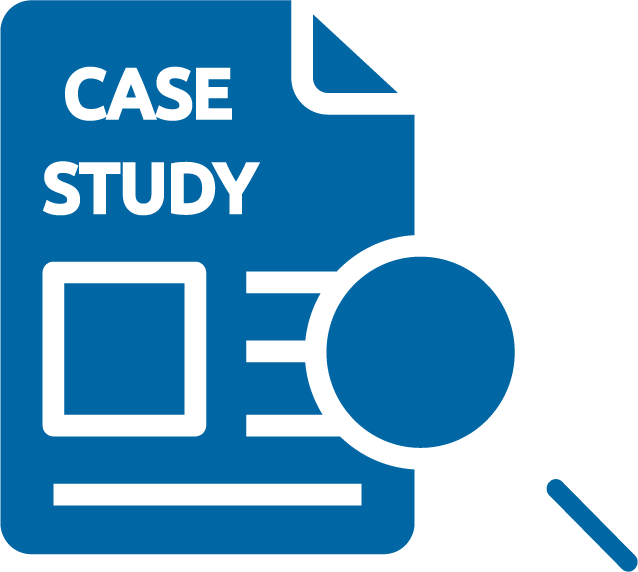
Gorman-Rupp Pumps with Additional Coatings Increase Abrasion Resistance in Scale Pits
How We Saved a Rolling Mill Customer $130K per Year with Gorman-Rupp Pumps
The Challenge
Reusing Process Water Containing High Solid Loads
The customer is a part of the world's leading integrated steel and mining company. This rolling mill manufactures special-grade and merchant bars reinforcing steel bars (rebar) and other semi-finished steel products. To minimize water consumption and reuse as much process water as possible in their manufacturing process, the customer sent all water back into a sump. Screens separate this sump into various settling pits (basins) to prevent solids from being pumped back into the system (process).
The customer's original pumps in hardened metals kept failing, causing significant downtime that reduced the mill's productivity. Additionally, the cost to replace the pumps was incredibly high (up to $35K). They needed a reliable, durable pump solution to withstand highly abrasive fluids.
The Solution
Self-Priming Pumps with Additional Coatings to Increase Abrasion Resistance
Our pump application expert offered a Gorman-Rupp T10 Series self-priming pump to replace their original pump. The T10 series was built with a gray iron casing, and we applied a two-component coating system to all wetted components for improved erosion-corrosion resistance. The ceramic-filled epoxy coating ensures more extended durability on all wearing parts to handle this high solid-loading slurry.
Other advantages include the following:
- They are self-priming, making them more efficient for intermittent pumping.
- They are more accessible to service, which cuts down on maintenance downtime.
- The worn components are replaceable, so the customer doesn't have to overhaul the pump regularly.
- The coating can be re-applied on all wetted parts.
The Result
A 300% increase in uptime and $130K cost savings per year
The customer rented the T10 unit for over a year without a single failure, making it a significantly better investment than the pumps they had been using from one of our competitors. The competitor's pump lasted 3-8 months before failure, so they saw a 300% increase in their equipment lifetime.
The original pump cost $28-$35K, so the customer could spend between $ 35K- $ 140K/year on replacement pumps. The GR T10 pump costs $35K all-in, but with the replaceable wear components, replacement parts and service costs are only around $10K/year. The final result was a 92% (or $130K) decrease in replacement costs per year.
Centrifugal Pump Technology Used
We solved the customer's problems using a Gorman-Rupp Super T Series self-priming centrifugal pump Model T10A60S-B.
How Self-Priming Pumps Works
Resources
Talk to one of our Experts
Reach out to our team of Spraying, Pumping, Filtering, Valve, and Systems Specialists today. We know we can help you with any municipal or industrial application challenges.