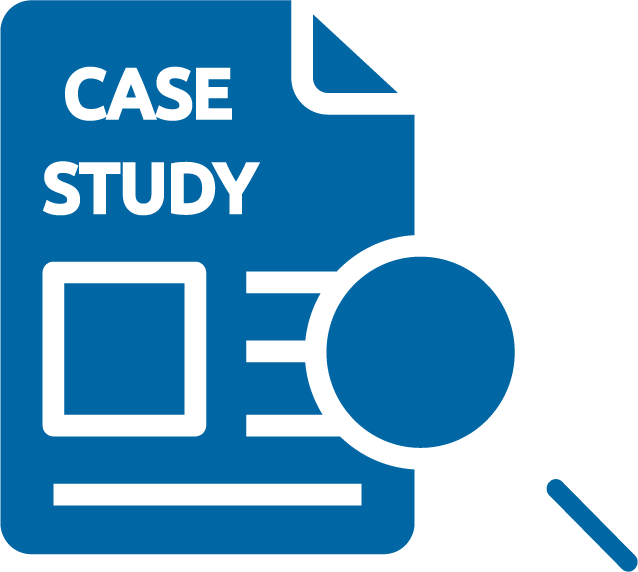
EATON DCF 1600 Mechanically Cleaned Filter for Calcium Sulfonate Grease Filtration
Specialty Chemicals Manufacturer Embraces Automation with a Mechanically Cleaned Filter Solution and Increases Productivity, Reduces Waste and Saves Money.
The Challenge: Retiring a Manual Filtration Process for Calcium Sulfonate Grease
The customer is a global developer and manufacturer of specialty chemicals that are used in a myriad of industries. This particular challenge involved filtering calcium sulfonate grease. The operations manager of the company wanted to improve their filtration process to:
- Optimize efficiency,
- Reducing downtime (filter change-out frequency),
- Make maintenance easier,
- And lower product waste.
The customer traditionally employed manual filtration to filter grease, which used bag housing and polyester multifilament bags rated for 600um. This filtration required a lot of maintenance, which meant downtime hindered productivity.
Additionally, sometimes bags weren’t able to handle high backpressure, which led to damaged bags, dirty products bypassing the filtration housing, and equipment damage downstream.
The customer’s requirements we were tasked with solving included:
- Eliminating manual filtration,
- Achieving finer filtration (75um),
- Reducing product waste,
- Eliminating bag disposal (environmentally friendly solution),
- And ensuring the solution wasn’t labour intensive.
The Solution: A Mechanically Cleaned Filter
Our filtration experts consulted with the customer to upgrade the filtration equipment at the facility, and they ultimately selected the Eaton mechanically cleaned DCF 1600 filter as the solution for this application.
During this consultation process, it also came to our attention that the grease was highly viscous, and it took a long time to pass through 2’’ pipe and into the housing. We changed the piping from 2’’ to a 3’’ connection for faster operation, and we offered the DCF-1600 rental unit to the customer on a trial basis to compare performance.
Post-Installation Challenge
The trial was successful and the customer purchased the Eaton DCF-1600 unit. Several months after the customer purchased the new unit, they reported a plugging problem to us. After some investigation we identified that, during production, the grease would start to cool down and thicken, making it harder to filter, clean, and purge.
When they were running a new batch, the grease inside the unit took much longer to heat, and it was negatively impacting the operation time as well.
How did we fix it?
After the customer reported the plugging issue and informed us of the temperature-sensitive nature of the grease, our application experts collaborated on a solution with the Eaton team. Eventually, we settled on Steam Jacketed housing because the steam circulating through the jacket around the filter housing would maintain the high temperature inside and prevent the grease from thickening.
The Result: Reduced Waste and Increased Filtration Efficiency
The maintenance crew on-site was happy with the technology. It reduced maintenance time, eliminated bag disposal, trimmed down product waste, and decreased product damage downstream. The operations manager was impressed by our customer service, in-depth knowledge of filtration products, and competence in dealing with the application challenges. As a result, John Brooks became his “go-to” filtration supplier of choice.
In short, with the DCF unit, we helped the customer:
- Eliminate media replacement,
- Reduce labour and maintenance costs,
- Increase consistency in solids removal,
- Reduce product loss,
- And increase production of a better, cleaner product.
Filter Technology Used
We solved the customer’s problems using an Eaton Mechanically Cleaned Filter – DCF 1600 with a 75um screen and a steam-jacketed housing.
Eaton Self-Cleaning Filter Specs
- Single unit weight: 215 lbs (97.5 kg)
- Service height: 102 in (259 cm)
- Total volumetric capacity: 11 gal (41.6 L)
- Purge chamber capacity: 5 gal (6 L)
- Filtration service area: 610 in² (3935 cm²)
- Flow rate range (at 100 μ): 60 to 200 gpm (13.6 to 45.4 m3/hr)
- temperature: 350 ˚F (177 ˚C)
- pressure: 150 psi (10.5 bar) standard
- air for actuator drive: 80 psi at 5 cfm (5 bar @ 8.5 m3/min)
- Voltage requirements: 110/220V, 50/60 Hz, single phase
How Self-Cleaning Filters Work
- The process begins as the unfiltered fluid enters the inlet of the cylindrical stainless-steel housing unit containing the filter screen. As the liquid passes through the filter, the screen catches the solids floating in the fluid and keeps them inside the housing unit while the fluid exits the outlet.
- The screen inside the housing requires cleaning to continue to filter optimally. The DCF 1600 has a unique spring-loaded cleaning disc that moves up and down the housing, cleaning the media and concentrated solids in both strokes.
- Once the slotted screen is cleared of debris, the cleaning disc directs the contaminants to the bottom of the housing and out of the flow path. This cleaning process happens while the filter remains in service, thereby maintaining the efficiency of the process and reducing the loss of valuable product.
- Because of the unique temperature requirements for this application, we used steam jacketed (SJ) housing for the filter. SJ housings are best used for applications where the fluid must be kept hot to remain fluid, e.g., applications like chocolate, asphalt, resins, and polymers. The housing body maintains the fluid’s temperature by circulating steam or a heat transfer fluid through the jacket on the housing, handling steam pressure up to 100 psi.
Talk to one of our Experts
Reach out to our team of Spraying, Pumping, Filtering, Valve, and Systems Specialists today. We know we can help you with any municipal or industrial application challenges.