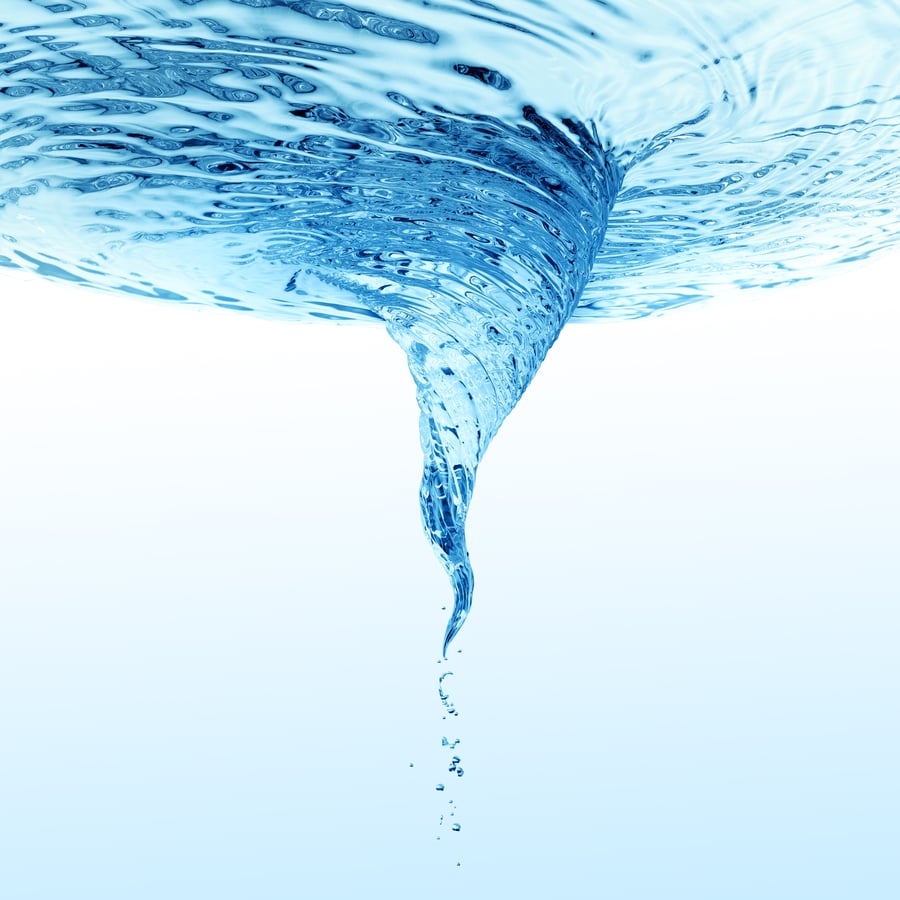
WHAT IS VORTEXING?
Vortexing occurs when a liquid's surface is drawn too close to an inlet pipe, causing air to enter the system. This suction causes a visible whirlpool on the surface of the liquid to form. This fluid motion typically occurs when there is free surface or air entrainment in the fluid. This motion causes the fluid to rotate around a central axis.
A low-pressure zone forms at the center of the vortex, known as cavitation, forming bubbles. These bubbles travel through areas of higher pressure and can cause erosion and pitting of the impeller and other components.
What are the signs of air entrainment?
Air entrainment draws air into the liquid as it swirls around the inlet, creating a vortex. This can lead to problems such as reduced efficiency, increased noise, and damage to the impeller.
- A visible whirlpool appears on the fluid's surface
- There are rapid fluctuations in the pump system's pressure gauge values.
- The pump has a reduced amperage draw
- There is a reduction in the overall flow rate
What Applications Can Cause Vortexing?
Vortexing can occur in any application where a pump moves fluids containing solids, fibres, or other materials. Selecting a pump design that is suited to the pumped fluid is necessary. This will reduce vortexing and ensure proper functioning. Here are some examples:
- Industrial processes involve pumping fluids that contain solids or slurries, such as mining, chemical processing, and wastewater treatment.
- Water and wastewater treatment, such as raw sewage pumping, can contain solids, debris, and fibrous materials.
- HVAC systems can cause vortexing in heating, ventilation, and air conditioning (HVAC) systems during the pumping of water or other fluids. This can cause air pockets to form in the design, reducing flow and system inefficiencies.
- Food and beverage processing often requires pumping liquids containing solids or fibres. Examples include fruit juice processing, dairy processing, and beer brewing.
How to Prevent a Vortex
To prevent a Vortex, reduce the inlet velocity by increasing the inlet diameter. Reducing the inlet velocity will allow the liquid level to be drawn down lower before Vortexing occurs.
In addition, pumps are often designed with specific features such as vortex impellers or anti-vortex plates. The impellers are designed to direct fluid flow away from their center. Plates are used to block the formation of a vortex. These plates create a barrier between the fluid surface and the impeller.
Vortexing can affect submersible pumps. Generally, the minimum submergence is determined by the need for the surrounding liquid to cool the motor, not by air entrainment.
For example, for the Gorman-Rupp Super T-Series:
Recommended Minimum Suction Line Submergence vs Velocity Chart in Vortexing
John Brooks Company is Your Prime SOurce for Pumps
John Brooks Company partners with world-renowned manufacturers to offer a variety of pumps for a broad range of commercial, municipal, and industrial uses, such as agriculture, food production, oil and gas, and mining. Our experts are available to assist you in selecting the right pump for your specific requirements.
Contact us now to explore what we have to offer or speak to one of our specialists.